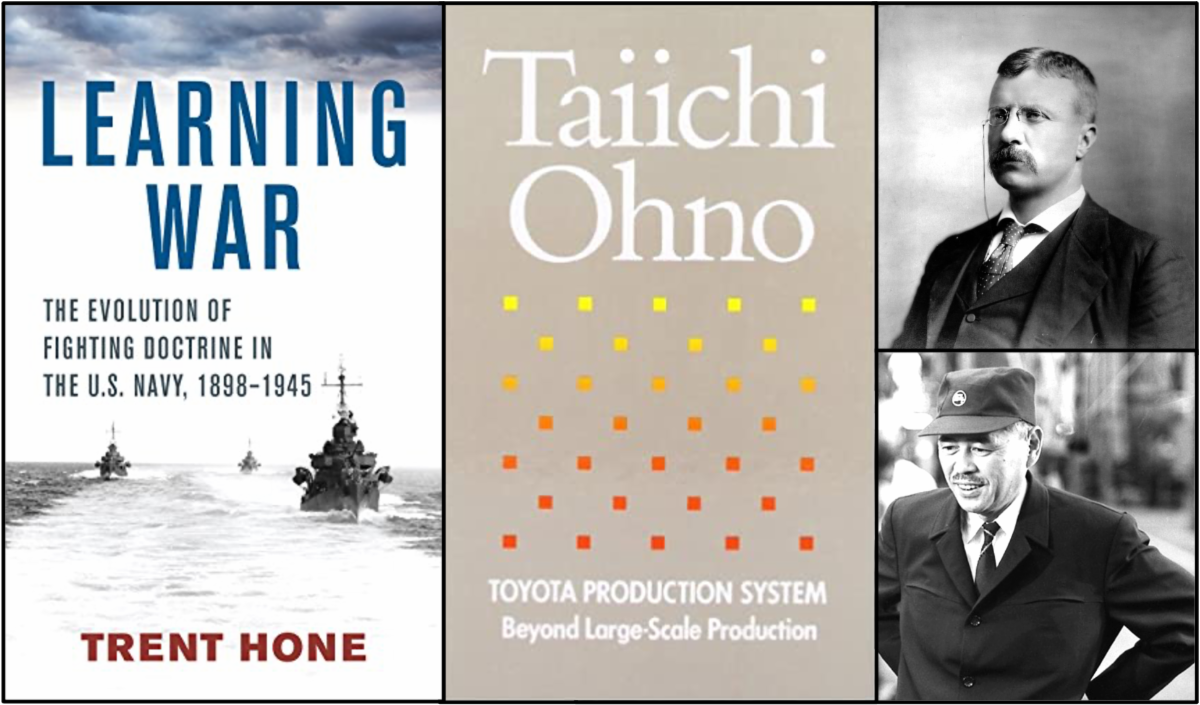
I was re reading “Learning War,” by Trent Hone, and page 30 and 31, it hit me, in the section about “engineering officers.” The pre condition (late 1800s early 1900s) was that there were line officers with everyone else (including engineering) in support. But with the shift from wood to steel and sails to steam, it was no longer possible to command without competent understanding of the technology being used to complete the mission. The technological was too integral to the tactical. Trent Hone quotes Teddy Roosevelt: “Every officer on a modern war vessel in reality has to be an engineer whether he wants to or not. Everything on such a vessel goes by machinery, and every officer, whether dealing with the turrets or the engine room, had to do with engineers’ work. There is no longer any reason for having a separate body of engineers responsible for only a part of the machinery. What is needed is one homogeneous body, all of whose members are trained for the efficient performance of the duties of the modern line officer. The midshipmen will be grounded in all these duties at Annapolis…We are not making a revolution, we are merely recognizing and giving shape to an evolution.” We could paraphrase this quote to Taichi Ohno and as reason he wrote his book about the Toyota Production System, published in English, thanks to Norman Bodek in 1988, but first published in 1978 in Japanese. [see an earlier note in which I discuss Ohno’s book and Jeffrey Liker’s Toyota Way.] Why 1978? Because in 1958, Toyota was arguably one of the worst auto companies in the world, designer and producer of the ToyoPet, a joke of a vehicle, made with some 1/8th the productivity typical around the world, and riven by labor-management strife. By 1978, Toyota (still unbeknownst to too many others) was the premier auto maker in the world, with defect rates 1/100th the world standard and productivity double. It was already on the way to cutting in half the time and the engineering effort needed for a major model upgrade. It’d been 20 years of evolving a management system that was demonstrably more effective and efficient at creating conditions in which individuals could give fuller expression to their innate creativity and in which individual effort could be more harmoniously integrated towards common purpose. They’d created the code and Ohno realized it was necessary to start documenting it. So, what would Ohno have said in Roosveltian terms? “Every manager of a modern design or production facility in reality has to be a (human) systems engineer whether they want to or not. Everything in such an organization goes by creativity and the relentless solving of hard problems, and every manager, whether dealing with the production cells or design studies, had to do systems engineering work of creating conditions in which it’s possible for people, individually and collectively and collaboratively, to give fullest expression to the creative potential. There is no longer any reason for having a separate body of managers and technicians responsible for only a part of the enterprise processes by which work gets done. What is needed is one homogeneous body, all of whose members are trained for the effective and efficient performance of the duties of the modern manager. Toyota leaders will be grounded in all these duties at throughout their development, periodically stepping outside day to day management responsibilities to learn how to cultivate their own design and problem solving capabilities, then those of shop floor personnel, and then how to teach their direct reports to cascade such capability through the ranks and across the enterprise …We are not making a revolution, we are merely recognizing and giving shape to an evolution that industrial organizations are increasingly complex in their work, dynamic in their situation, and subject to economic and competitive challenges for which they must be prepared to address.” As for rules, tools, and application… Engineering education differed from skilled trade and artisan training. Skilled tradespeople and artisans learn experientially, develop skill and competency iteratively and intuitively, and achieve mastery with skills that are often tacit. They develop protégés through a similar mentored process. The applied use of tools becomes the basis for developing competency. Engineering education differs. It starts with “rules”—e.g., Newtonian mechanics, thermodynamics, fluid dynamics, ideal gas law, and heat transfer. The rules are first understood through rudimentary problems—e.g., single point masses, frictionless acceleration. Gradually tools are introduced by which the rules can be applied onto problems of increasingly complexity and difficulty. Eventually, mastery is achieved by the broad application of the rules via the tools onto a broad and diverse range of application. So too with the engineering of collaborative systems. As a trade, managers acquire the norms and habits characteristic of their work environment, demonstrating competency in adhering to those routines and cultural standards, and proving success by adhering to them with conviction and consistency. As a science, they’re taught the “rules” of how to construct systems that are more conducive to effective collaboration and harmonization: workflows that are simpler than complex, with (temporary, self correcting) standardization in lieu of improvisation, self-stabilizing to reduce aggravation and avoid local disturbances from escaping to become systemic ones, and self-synchronizing to maintain coordination across functions and disciplines. They’re taught how to solve problems in a rigorous, empirical fashion, and to systemize what’s discovered through recreation of (virtual) discovery. They acquire tools that are expression of those rules (e.g., simple by value stream maps, synchronization by just in time and pull), and they build competency through the repeated application of the rules onto a broad and diverse range of application. As with the engineer relative to the skilled crafts person, the (human) systems engineer is far more effective than the heuristics managers who, absent the “basic thinking” of trained professional, can operate only within the bounds of territory that is familiar and which has been well explored. |
Steven Spear DBA MS MS Principal, See to Solve LLC Senior Lecturer, MIT Sloan School of Management Senior Fellow, Institute for Healthcare Improvement Author, The High Velocity Edge |
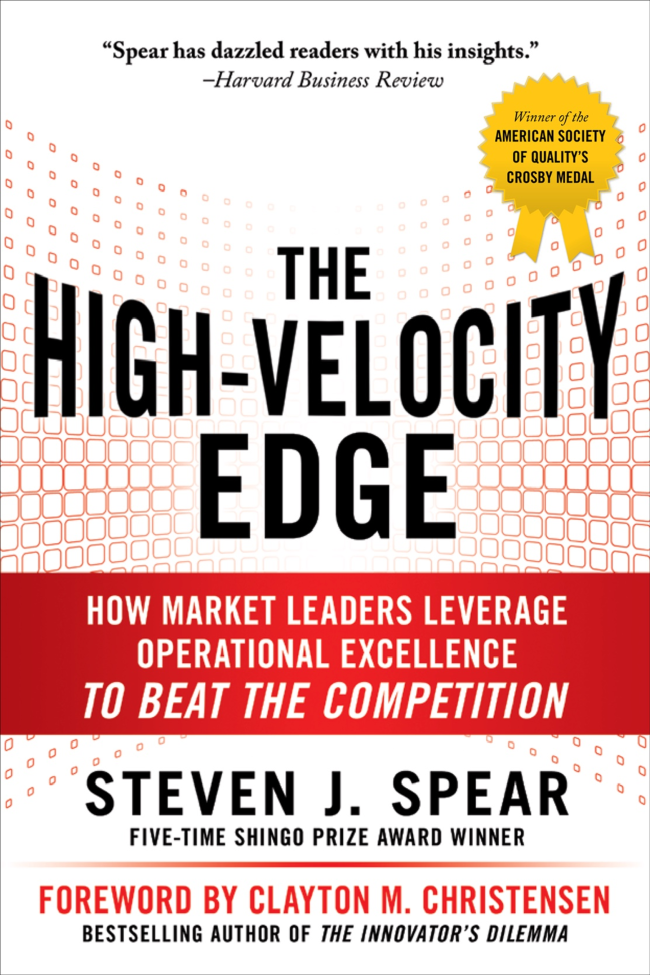
Click here for sample chapters from The High Velocity Edge • leadership and crisis recovery (chapters 9 and 10) • accelerating development of break through technologies (chapter 5) |